采用多层多道焊接,是根据什么来分道焊?
来源: 日期:2021-12-22 10:29:45 浏览次数:
焊脚尺寸小于8mm的焊缝,通常采用单层焊(一层一道焊缝)来完成,焊条直径根据钢板厚度不同在3~5mm范围内选择。
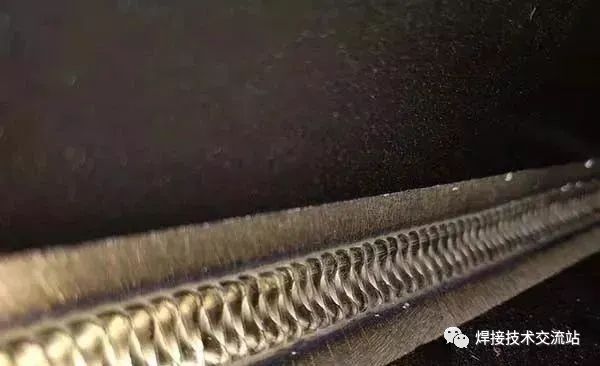
焊脚尺寸小于5mm的焊缝,可采用直线形运条法和短弧进行焊接,焊接速度要均匀,焊条角度与水平板成45°,与焊接方向成65°~80°的夹角。焊条角度过小会造成根部熔深不足;角度过大,熔渣容易跑到前面造成夹渣。
在使用直线形运条法焊接焊脚尺寸不大的焊缝时,将焊条端头的套管边缘靠在焊缝上,并轻轻地压住它,当焊条熔化时,会逐渐沿着焊接方向移动。这样不但便于操作,而且熔深较大,焊缝外表也美观。
焊脚尺寸在5~8mm时,可采用斜圆圈形或反锯齿形运条法进行焊接,但运条速度不同,否则容易产生咬边、夹渣、边缘熔合不良等现象。
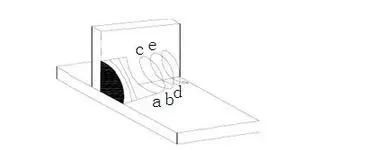
如图2-9所示,a点至b点运条速度要稍慢些,以保证熔化金属与水平板很好熔合;b点至c点的运条速度要稍快些,以防止熔化金属下淌;
当从b点运条到c点时,在c点要稍作停留,以保证熔化金属与垂直板很好熔合,并且还能避免产生咬边现象;
c点至b点的运条速度又要稍慢些,才能避免产生夹渣现象及保证根部焊透;
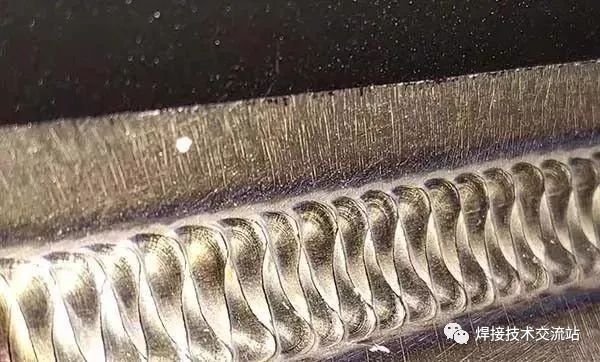
b点至d点的运条速度与a点至b点一样要稍慢些;d点至e点与b点至c点相同, e点与c点相同,要稍作停留。
整个运条过程就是不断重复上述过程。同时在整个运条过程中,都应采用短弧焊接。这样所得的焊缝才能宽窄一致,高低平整,不产生咬边、夹渣、下垂等缺陷。
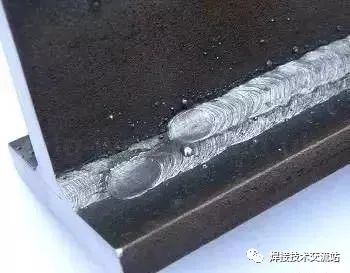
焊第一层时,可采用3~4mm直径的焊条,焊接电流稍大些,以获得较大的熔深。采用直线形运条法,在收尾时应把弧坑填满或略高些,这样在焊接第二次收尾时,不会因焊缝温度增高而产生弧坑过低的现象。
在焊第二层之前,必须将第一层的熔渣清除干净,如发现有夹渣,应用小直径焊条修补后方可焊第二层,这样才能保证层与层之间紧密的熔合。在焊第二层时,可采用4mm直径的焊条,焊接电流不宜过大,电流过大会产生咬边现象。
用斜圆圈形或反锯齿形运条法施焊, 具体运条方法与单层焊相同。但是第一层焊缝有咬边时,在第二次焊接时,应在咬边处适当多停留一些时间,以弥补第一层咬边的缺陷。
当焊接焊脚尺寸大于10mm的焊缝时,如果采用多层焊,则由于焊缝表面较宽,坡度较大,熔化金属容易下垂,给操作带来一定的困难。所以在实际生产中都采用多层多道焊。
焊脚尺寸为10~12mm时,一般用两层三道来完成。焊第一层(第一道)时,可采用较小直径的焊条及较大焊接电流,用直线形运条法,收尾与多层焊的第一层相同。焊完后将熔渣清除干净。
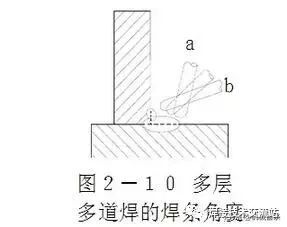
焊第二道焊缝时,应覆盖不小于第一层焊缝的2/3,焊条与水平板的角度要稍大些(图2-10中a),一般为45°~55°,以使熔化金属与水平板很好熔合。
焊条与焊接方向的夹角仍为65°~80°,用斜圆圈形或反锯齿形运条,运条速度除了在图2-9中的c点、e点上不需停留之外,其他都一样。焊接时应注意熔化金属与水平板要很好熔合焊接第三道焊缝时,应覆盖第二道焊缝的1/3~1/2。
焊条与水平板的角度为40°~45°(图2-10中的b),角度太大易产生焊脚下偏现象。一般采用直线形运条法,焊接速度要均匀,不宜太慢,因为速度慢了容易产生焊瘤,使焊缝成形不美观。
当第二道焊缝覆盖第一层大于2/3时,在焊接第三道时可采用直线往复运条法,以避免第三道焊缝过高。
如果第二道覆盖第一道太少时,第三道焊接时可采用斜圆圈运条法,运条时在垂直板上要稍作停留,以防止咬边,这样就能弥补由于第二道覆盖过少而产生的焊脚下偏现象。
如果焊接焊脚尺寸大于12mm以上的焊件时,可采用三层六道、四层十道来完成, 如图2-11所示。
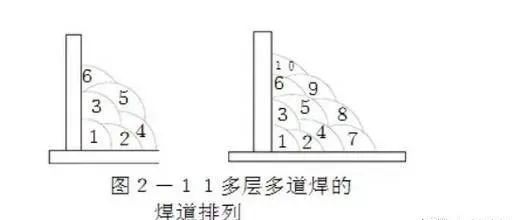