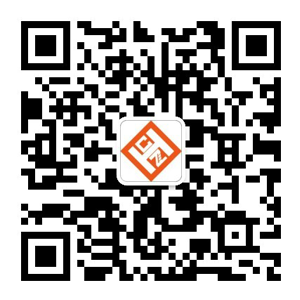
1搅拌摩擦焊概览
搅拌摩擦焊(Friction Stir Welding,FSW)作为一种固相连接技术,在1991年由英国焊接研究所(The Welding Institute, TWI)发明[1]。与传统熔化焊相比,FSW无需添加焊丝、不需要保护气体,焊接过程无污染、无烟尘、无辐射,焊接接头残余应力低,因此具有焊接效率高、焊接变形小、能耗低、设备简单、焊接过程安全等一系列优点[2-4]。经过20多年的发展,FSW已经在航空航天、轨道交通、舰船等领域得到了广泛应用[3-6]。
搅拌摩擦焊的原理如图1所示。高速旋转的搅拌头扎入被焊工件内,旋转的搅拌针与被焊材料发生摩擦并使其发生塑化,轴肩与工件表面摩擦生热并用于防止塑性状态的材料溢出。在焊接过程中,工件要刚性固定在背部垫板上,搅拌头边高速旋转边沿工件的接缝与工件相对移动,在搅拌头锻压力的作用下形成焊缝,最终实现被焊工件的冶金结合。
图1 搅拌摩擦焊接原理
搅拌摩擦焊广泛适用于各类材料,目前已成功实现了铝、镁等低熔点金属及合金、铜合金、钛合金、钢铁材料、金属基复合材料以及异种金属(铝/铜、铝/镁、铝/钢等)的焊接。
在传统技术的基础上,搅拌摩擦焊有了五大创新发展:双轴肩搅拌摩擦焊、静轴肩搅拌摩擦焊、搅拌摩擦点焊、复合能场搅拌摩擦焊、搅拌摩擦增材制造。
双轴肩搅拌摩擦焊(Bobbin Tool Friction Stir Welding,BT-FSW)与传统FSW相比,其搅拌头为上、下轴肩结构,两个轴肩通过搅拌针连接,下轴肩取代了传统FSW的背部刚性支撑垫板,对工件进行自支撑,实现中空部件的焊接。其焊接原理如图2所示。上、下双轴肩的结构在焊接过程中降低了接头厚度方向的温度梯度,减小了接头组织不均匀性,可实现根部全焊透的焊接[7]。
图2 双轴肩搅拌摩擦焊接原理
1.上轴肩 2.前进侧 3.熔合线 4.后退侧 5.工件 6.搅拌针 7.下轴肩
静轴肩搅拌摩擦焊(Stational Shoulder Friction Stir Welding,SS-FSW)采用轴肩与搅拌针分体式设计,在焊接过程中内部搅拌针处于旋转状态,而外部轴肩不转动,仅沿焊接方向行进。在常规FSW中,轴肩与被焊接材料之间的摩擦是主要的产热方式。相比之下,静轴肩搅拌摩擦焊由于内部搅拌针转动而外部轴肩不转动,所以搅拌针在摩擦生热和材料变形中起着重要的作用[8]。
与常规FSW相比,静轴肩搅拌摩擦焊的焊缝成形良好,表面粗糙度能达到母材的水平,并且可以实现角焊缝等非平面结构构件的搅拌摩擦焊接,如图3所示。
图3 静轴肩角接焊缝
搅拌摩擦点焊与常规FSW原理相似,缺少了搅拌针与被焊工件相对移动产生焊缝的过程,取而代之的是,依靠旋转下压的搅拌头与工件接触摩擦产生热量,经充分搅拌后形成单个焊点。搅拌摩擦点焊可分为两类:传统直插式和回填式。
传统直插式搅拌摩擦点焊包括扎入、旋转、拔出三个过程,焊接完成后在焊点处会留下一个匙孔。其焊接示意如图4所示。
图4 直插式搅拌摩擦点焊示意
回填式搅拌摩擦点焊采用特殊的焊接工具,包括搅拌针、搅拌套、压紧环。通过精确控制搅拌头各部件的相对运动,在搅拌针回撤的同时填充搅拌头在焊接过程中形成的匙孔缺陷。其焊接过程包括搅拌套扎入、搅拌针拔出、搅拌套拔出及搅拌针回填,最终得到表面平整的焊点[9]。
复合能场搅拌摩擦焊是指在焊接过程中施加额外的能量场(感应加热、激光、电弧、超声等),以达到降低焊接载荷,延长搅拌头寿命,改善焊缝组织,实现高熔点材料焊接等目的。
搅拌摩擦增材制造实质为多层材料的焊合叠加,其增材过程类似于FSW搭接,与搅拌摩擦增材制造搭接不同的是,搅拌摩擦增材制造是材料的多层多次搭接,是一个空间搭接的过程,包括垂直于搭接方向的横向增材和平行于材料厚度方向的增材[10],搅拌摩擦增材制造过程如图5所示。
图5 搅拌摩擦增材制造过程
2搅拌摩擦焊技术应用
近年来,我国搅拌摩擦焊技术的应用得到了较大发展,在航空航天、轨道交通、船舶以及电力电子等方面都有了长足的进步。
自 2005 年开始,针对飞机结构及材料,国内开展了搅拌摩擦焊基础工艺技术研究,并与国内飞机设计所和制造厂合作,积极探索搅拌摩擦焊应用于在役和未来新一代战斗机、大飞机的可行性。图6为中国搅拌摩擦焊中心研制的搅拌摩擦焊薄壁飞机模拟结构件[6]。
图6 搅拌摩擦焊薄壁飞机模拟结构件
基于搅拌摩擦焊在航天铝合金结构产品制造上的优越性和新型空间运载工具发展需要,中国搅拌摩擦焊中心于“十五”期间重点对航天运载火箭箭体结构搅拌摩擦焊进行了研究开发,同时为了适应国际航天焊接技术发展趋势, 国内的航天制造企业也积极采用搅拌摩擦焊用于航天贮箱结构焊接,图 7为2004年中国搅拌摩擦焊中心焊接的铝合金燃料贮箱筒段模拟验证件。
图7 铝合金燃料贮箱筒段模拟验证件
在国内, 搅拌摩擦焊作为推进剂贮箱的一项关键制造工艺,正在深入进行工程化应用研究。搅拌摩擦焊在航天工业上的应用和推广,可以提高中国航天运载工具及导弹类产品的性能和生产效率,为国防、载人航天及探月工程等做出贡献。
与航空航天类似,搅拌摩擦焊在轨道交通以及船舶上的应用主要也是结构件的生产制备。比如列车车身壁板、驱动箱、船甲板、汽车车门、轮毂等。图8为搅拌摩擦焊加工轨道列车的车身壁板和轮船壁板。
图8 搅拌摩擦焊加工轨道列车车身壁板和轮船壁板
而在电力电子方面,搅拌摩擦焊技术主要应用在中空热沉器、散热器及传感器等。采用搅拌摩擦焊加工的电力行业所需的水冷散热器如图9所示。
图9 水冷散热器
3机器人搅拌摩擦焊
要想实现搅拌摩擦焊生产与制备各种产品的目的,搅拌摩擦焊设备是至关重要的部分。搅拌摩擦焊设备主要分为三类:龙门式搅拌摩擦焊设备、搅拌摩擦焊专机和机器人搅拌摩擦焊设备。
3.1传统的搅拌摩擦焊设备
龙门式搅拌摩擦焊设备具有刚度大、可焊工件厚度大、焊接稳定性强、焊接效率高等技术特点。龙门式搅拌摩擦焊设备如图10所示。
图10 龙门式搅拌摩擦焊设备
搅拌摩擦焊专机即为特定尺寸、结构或功能定制的设备。火箭燃料贮存箱搅拌摩擦焊专机如图11所示。
图11 火箭燃料贮存箱搅拌摩擦焊专机
3.2机器人搅拌摩擦焊设备
传统的龙门式搅拌摩擦焊设备只能完成直线或平面二维焊接要求,不能满足复杂结构件的焊接,工业机器人具有较高的柔性,可以实现复杂轨迹运动,使复杂结构件的焊接成为可能。机器人搅拌摩擦焊接技术可提升焊接自动化程度和生产效率,其技术优势和社会经济效益显著。
机器人搅拌摩擦焊设备因为焊接适应性强、易于实现空间全位置焊接、自动化程度高、生产效率高等技术特点,近年来得到了越来越多地应用。
机器人搅拌摩擦焊技术与装备已成为当前国际搅拌摩擦焊技术研发热点,并得到了国内外焊接工程技术人员和工业用户的广泛关注。
当前机器人搅拌摩擦焊技术,亟待解决以下几方面关键技术:
1)适用于搅拌摩擦焊接的重载工业机器人本体设计与制造技术。实现机器人搅拌摩擦焊的基本条件是机器人本体承载能力必须很高,通常>500kg,而且对于机器人在高载荷作业条件下的工作稳定性、重复定位精度、空间位置和姿态规划都提出了很高的要求。
2)机器人搅拌摩擦焊机头的设计与制造是机器人搅拌摩擦焊系统集成和功能实现的关键。机器人搅拌摩擦焊机头需要集成复杂的测控系统,包括:压力测控系统、温度测控系统、焊缝跟踪系统、三维激光定位系统和焊接过程冷却与润滑系统等;同时为了提高机器人运动的灵活性和可达性,需要焊接机头尽可能地减小体积。
3)机器人搅拌摩擦焊控制模块是保证焊接过程稳定性的重要因素,是机器人搅拌摩擦焊复杂曲面焊接可靠性的重要保障。机器人搅拌摩擦焊接过程控制传感器主要包括三维定位、压力、位移、温度、焊缝跟踪等,通过通信模块和总线将系统与传感器连接在一起,并实时采集数据由系统进行分析,再由通信模块输出进行焊接轨迹、姿态及工艺参数修正,最终达到精确控制的目的。
4)通过确定搅拌摩擦焊标准化流程,组织并有效协同路径规划、校准、过程模拟、过程控制、焊接工艺模块等各子系统,实现机器人搅拌摩擦焊系统集成,开发适用于搅拌摩擦焊接的机器人软件包。
5)当前工业产品多具有小批量多品种特征,要求生产线具备柔性制造能力。采用工业机器人进行搅拌摩擦焊时,对焊接顺序及作业路径必须进行工艺规划,并通过离线编程实现干涉检测和指令生成,而且必须结合前序生产过程实时信息,对后续加工过程进行同步调整,以充分发挥机器人在工业高效自动化生产中的优势。
3.3重载机器人搅拌摩擦焊系统
广东省焊接技术研究所(广东省中乌研究院)基于载重1t的KUKA工业机器人,集成了具有自主知识产权的重载机器人搅拌摩擦焊系统。通过机头的设计与制造、应用软件系统开发、焊接过程稳定性研究与焊接工艺研究等过程,实现了产品开发与标准制定的目标,并且采用所开发的搅拌摩擦焊接系统进行了产品的加工生产,成功实现产业化应用。
(1)机头的设计与制造 机头的设计即主轴系统的结构设计。系统包括高速电主轴、压力传感器、激光跟踪器、冷却系统、搅拌头和刀柄、转接盘等连接配件。其实物如图12所示。
图12 主轴系统实物
注:①为力学传感器,②为高速电主轴,③为激光跟踪器,
④为油冷系统,⑤为搅拌头,⑥为刀柄。
高速电主轴提供搅拌头旋转摩擦动力,名义最高转速6000 r/min,扭矩55Nm;压力传感器呈120°圆周对称分布,用于实时监测焊接下压力,量程0~20kN;激光跟踪器设置于焊接前端,用于对焊缝进行扫描跟踪,检测精度<0.2mm;冷却系统保证焊接过程中的热量输入不会过大,延长搅拌头和搅拌工具的使用寿命;搅拌头即搅拌摩擦焊接工具,用于焊缝成形,可根据不同焊接需求定制加工。
(2)机器人焊接工艺研究 经过焊接过程稳定性的研究后,对机器人焊接工艺展开了相关研究工作。主要包括一维常规FSW、一维静轴肩FSW、一维搅拌摩擦点焊和二维FSW、三维复杂曲面的搅拌摩擦焊接工艺研究。
研究内容主要包括:焊接参数的确定与优化、接头宏观形貌与微观组织观察以及力学性能测试分析。
采用常规搅拌头对4mm厚1561铝合金进行焊接试验。转速600~2200r/min,焊接速度200mm/min,固定压力恒定7500N。焊接过程稳定,压力震动幅值<8%。均获得了成形良好的焊缝,最优接头抗拉强度达母材的99%,如图13所示。
图13 接头抗拉强度与转速关系
采用自主开发的高转速静轴肩搅拌摩擦焊专用工具对4mm厚2219-T6铝合金进行试验。转速2000~2600r/min,焊接速度100mm/min。通过观察不同位置处焊缝表面形貌和接头宏观形貌(见图14、图15),可知静轴肩搅拌摩擦焊显著提高了焊缝表面质量。
图14 焊缝表面形貌
图15 接头宏观形貌
采用恒压力及恒位置模式对(2+2)mm厚6061-T6铝合金进行搅拌摩擦点焊对比试验。转速在1000~1500r/min内改变,均获得了良好的焊点成形。采用恒位移焊接模式所得最优接头拉剪性能为2400N,采用恒压力焊接模式所得最优接头拉剪性能提升至4000N。
同时,采用恒压力及恒位置模式对二维搅拌摩擦焊工艺进行开发。在4mm厚6061-T6铝合金板上,成功实现二维转角搅拌摩擦焊(见图16),试验中发现,采用恒压力模式可显著提高焊接稳定性。
a)恒压力 b) 恒位置
图16 恒压力及恒位置模式二维转角搅拌摩擦焊
进一步采用所开发的机器人搅拌摩擦焊接系统成功实现了复杂曲面的高质量搅拌摩擦焊接。工件模型和焊缝成形情况如图17所示。
图17 曲面焊缝成形
经过大量的试验和研究,采用所开发的搅拌摩擦焊接系统成功地进行了新能源汽车电池托盘、水冷散热器、手机外壳的加工生产,并实现产业化应用。其中,针对电池托盘,其综合焊接效率由龙门式搅拌摩擦焊设备的65 PCS/8h提高到91 PCS/8h,提高了约40%,并具有进一步提高的空间。
4结束语
1)搅拌摩擦焊工艺由于其自身的技术特点,在有色金属领域有着广阔的应用前景。
2)国产机器人搅拌摩擦焊接系统完全可以满足应用场景中的技术要求,实现稳定的焊接生产制造。
3)机器人搅拌摩擦焊接是未来搅拌摩擦焊装备发展的一个重要方向,随着重载机器人国产化,机器人本体价格将大幅下降,从而使得机器人搅拌摩擦焊装备更加广泛的应用,更开放的控制系统。
参考文献:
[1]Thomas W M, Nicholas E D, Needham J C, et al. Friction stir butt welding, International Patent Application no[J]. PCT/GB92 Patent application, 1991 (9125978.8).
[2]张华, 林三宝, 吴林, 等. 搅拌摩擦焊研究进展及前景展望[J]. 焊接学报, 2003, 24(3): 91-96.
[3]吴安如, 夏长清, 王少武, 等. 搅拌摩擦焊接技术的研究现状及其展望[J]. 材料导报, 2005, 19(4): 85-88.
[4]任淑荣, 马宗义, 陈礼清. 搅拌摩擦焊接及其加工研究现状与展望[J]. 材料导报, 2007, 21(1): 86-92.
[5]Mishra R S, Ma Z Y. Friction stir welding and processing[J]. Materials Science and Engineering: R: reports, 2005, 50(1-2): 1-78.
[6]董春林, 栾国红, 关桥. 搅拌摩擦焊在航空航天工业的应用发展现状与前景[J]. 焊接, 2008 (11): 25-31.
[7]董继红, 聂绪胜, 鄢江武, 等. 常规FSW与双轴肩FSW对铝合金接头组织和性能的影响[J]. 焊接学报, 2013, 34(7): 85 − 88.
[8]刘会杰, 李金全, 段卫军. 静止轴肩搅拌摩擦焊的研究进展[J]. 焊接学报编,2012,33(5): 108-112.
[9]杨洪刚, 赵欣. 铝合金回填式搅拌摩擦点焊工艺试验[J]. 焊接技术, 2012,41(11): 24-26.
[10]黄斌. 基于静轴肩搅拌摩擦焊的增材制造技术研究[D]. 南昌航空大学,2016.
微信:hanlinyuanApp 传真:(021)882899521 邮箱:hanlinyuanapp#qq.com
2017-2020版权所有 不得转载 黑ICP备2023002448号