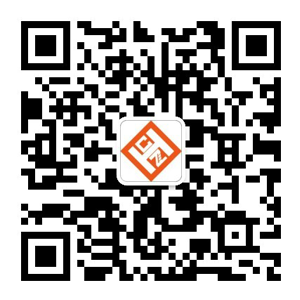
摘要:针对窄间隙焊接需要精确的焊缝偏差信息以保证焊枪对中的问题,设计了一套磁控电弧-激光传感器相结合的焊缝跟踪系统,由前置的激光视觉传感器扫描焊缝中心,采用形态提取算法和基于Kernel算法的相关滤波器得到焊缝特征点的坐标,经拉格朗日插值法处理,拟合出焊缝轨迹的近似曲线,设定门限阈值分两种情况采用双传感器数据自适应加权融合方法进行信息融合,使得焊缝偏差信息更为精确,最终保证焊枪的对中和侧壁良好融合。
前言 |
窄间隙MAG 焊是在大型压力容器、建筑构件、装备制造业等领域应用十分广泛的一种熔化极活性气体保护的厚板焊接方法。目前对窄间隙MAG焊的研究主要集中在焊接工艺及焊缝成形方面,焊缝跟踪系统的研究以磁控电弧传感器和激光传感器为主,现有焊缝跟踪传感器采集的是单一面的信息,难以克服焊接过程中各种不确定因素对焊缝偏差信息提取的影响,焊缝跟踪失败的可能性较大。将多种传感器有机结合是解决复杂环境下焊缝跟踪的有效途径,也是焊接自动化发展的必然趋势。多传感信息融合技术在军事运用方面取得了较大发展,但在自动化焊接系统的焊缝跟踪中研究较少。
在窄间隙的环境下采用磁控电弧传感器和激光视觉传感器同时对窄间隙焊接坡口进行跟踪识别,对采集到的数据进行信息融合,提出一种新的解决方案,并设计出相应的焊缝跟踪系统。通过试验证明在窄间隙焊接中,磁控电弧与激光视觉传感器的信息融合具有可行性和稳定性。
磁控电弧激光传感器焊缝跟踪系统及结构司简介
在窄间隙焊接过程中,磁控电弧传感器控制电弧摆动扫描坡口,霍尔传感器将实时检测到的电流信号经过滤波电路[1]和软件滤波处理,再经过A/D转换成数字量得到焊枪偏离焊缝中心的信息。激光传感器将激光投射在焊接坡口上,由图像采集装置采集含有焊缝偏差信息的激光条纹图像,经动态阈值处理与特征点检测可以得到焊枪偏离焊缝中心的信息。两种焊缝偏差信息采用双传感器数据自适应加权融合方法进行融合处理后输入到控制系统中,然后调整焊枪位置,实现焊枪的对中。其焊缝跟踪系统流程如图1所示。所设计的磁控电弧激光传感器重点考虑了窄间隙焊道坡口信息采集能力、抗外界干扰能力、高强工作条件的稳定性、普适性、经济性等问题,其结构设计如图2所示。
在磁控电弧激光传感器的左右两侧安装对称的励磁装置和温度检测装置,励磁装置由弯月形导磁软铁铁心和漆线线圈组成,铁心上端通过燕尾槽盖板,被燕尾槽滑块固定;在前置区域安装激光视觉传感器,由CMOS相机、激光传感器和滤光片组成,在后置位置安装激光辅助光源,以应对在窄间隙环境中光线较差的问题,通过固定装置固定在燕尾槽盖板上。整个传感器整体结构为扁薄状并将激光传感器结合为一体,大大减少了传感器的体积,更加适合窄间隙环境。
磁控-激光传感器工作原理 |
2.1激光传感器的工作原理
激光条纹类型如图3 所示,激光视觉传感器如图4所示。激光条纹类型分为单线激光条纹和多线激光条纹,本文采用三线激光装置作为视觉传感装置。三线激光发生器与工业相机之间的固定角度兹,传感器与被焊工件之间的距离为H,激光传感器的工作原理如下:首先,激光发生装置在焊接工件上照射出三线条纹;然后,利用漫反射原理在照相机的CMOS 传感器中成像激光条纹。拍摄的图像反映了焊缝的平面位置和焊缝角度的深度信息。
2.2 CMOS相机测距原理
建立相机坐标系OcXcYcZc、成像坐标系OIXIYIZI、像素坐标系OPXPYPZP,如图5所示。由于激光条纹图像反映了各点激光在工件表面投射点与CMOS 相机的距离,通过合适的图像处理算法可得到焊缝特征点的二维像素坐标,并通过一系列坐标转换关系可以倒推出该图象在绝对坐标系的位置坐标,从而实现焊缝对中。激光平面与工件平面相交形成的激光条纹中任意一点Q,设其在相机坐标系OcXcYcZc中的空间坐标为(xc,yc,zc),由于漫反射原理在成像坐标系OIXIYIZI 中坐标(x,y)处得到与之对应的像点Q',由小孔透视理论可知,在点的齐次坐标下可将上述投影规律表示为
式中k>0为投影尺度因子;f 为像方焦距;M 为透视投影矩阵。该式表示物点空间三维坐标(xc,yc,zc)
与像点坐标(x,y)之间的关系。
2.3初始焊接特征点的提取
由于噪声较小,采用形态提取算法可以计算焊缝特征点的坐标,特征点为初始参考位置。形态学提取的过程如下:①将采集信息采用动态阈值筛选,以去除低灰度级噪声;②对目标区域采用形态学处理;③进行骨架提取,得到亚像素级激光条纹;④将框架内的直线进行拟合得到2 条拟合直线;⑤将2条直线展开以获得所需特征点位置坐标。焊缝特征点的提取过程如图6所示。
基于高斯KCF 目标跟踪算法是一种用于快速和准确地确定噪声图像存在焊缝特征点位置的方法。因此,本研究采用基于Kernel算法的相关滤波器(KCF)实时检测焊缝特征点,可以快速准确地确定噪声图像中焊缝特征点的位置,保证系统的实时性能[2],得到焊枪偏离焊缝中心的信息。
2.4磁控电弧传感器工作原理
励磁电源对励磁线圈施加交变电流,产生平行交变磁场作用于电弧,使其在洛仑磁力的作用下进行摆动,进而扫描窄间隙焊接坡口,由霍尔传感器收集焊接电流变化信号,对其进行分析处理后得到焊枪偏离焊缝中心的信息。
2.5窄间隙焊缝轨迹预测
窄间隙的焊缝轨迹预测是在焊接时,通过前置的激光视觉传感器采集焊道信息后,将激光视觉传感器获取的所有焊缝特征点的位置坐标ai (xi,yi),采用拉格朗日插值法拟合出一条焊缝轨迹的近似曲线,由近似函数Fn (x)的表达式可计算出该段内所有拐点、极值点以及每一点处的曲率,是对后续焊接轨迹预测的过程[3]。拉格朗日插值法为
式中yi为焊缝特征点的纵坐标;xi为焊缝特征点的横坐标。
焊缝轨迹预测示意如图7 所示,x 轴代表焊缝中心位置,根据焊缝特征点的二维坐标采用拉格朗日插值法拟合出一条焊缝轨迹的近似曲线,并得到对应的近似函数Fn(x),焊缝轨迹的预测是信息融合方法的必要条件。
2.6信息融合方法
信息融合方法的要点是:由前置的激光视觉传感器提取焊缝轨迹特征,判断焊缝轨迹变化,在焊缝轨迹曲率较大或者拐点、极值点处,由实时性能较好的磁控电弧传感器获取更精确的焊枪偏离焊缝中心的值作为系统执行机构的纠偏量;而在焊缝轨迹曲率较小或者非拐点、非极值点情况下,采用激光视觉传感器与磁控电弧传感器数据自适应最优加权融合方法获取焊枪偏离焊缝中心的值作为系统执行机构的纠偏量。
其中,前置的激光视觉传感器扫描焊缝中心可以得到焊枪偏离焊缝中心的估计值,同时磁控电弧传感器扫描焊缝中心可得到焊枪偏离焊缝中心的实际值。焊缝偏差信息的估计值经拉格朗日插值法进行处理,拟合出焊缝轨迹的近似曲线并得到其近似函数,可求出该焊缝曲线的拐点、极值点并通过设定门限阈值对估计值进行可行性检验,根据检验结果分为以下两种情况进行数据融合:
(1)设Z为曲率门限阈值,当曲率k>Z或焊枪处于焊缝轨迹的拐点、极值点时,采用激光视觉传感器得到的焊缝偏差信息精度较低,故采用实时性能较好的磁控电弧传感器获取的焊缝偏差信息作为焊缝偏差的融合值。
(2)当曲率k
上述信息融合方法如图8 所示,设激光视觉传感器测量的焊缝偏差信息的估计值为X1、X2、……、Xn,磁控电弧传感器测量的焊缝偏差信息的实际值为Y1、Y2、……、Yn。激光视觉传感器的加权因子为W1、W2、……、Wn,磁控电弧传感器的加权因子为U1、U2、……、Un。激光视觉传感器的方差为V,磁控电弧传感器的方差为S,总均方差为啄,将两种传感器进行加权融合[4],得到焊缝偏差的融合值e。
联立以上三式,根据多元函数求极值理论,可求出总均方误差最小时所对应的加权因子W 和U,从而得到最优焊缝偏差的融合值e 。
焊接试验结果与分析 |
3.1焊接试验平台简述
试验参数为:选择直径1.2 mm焊丝,焊接速度设定5 mm/s,焊接电压14 V,电流220 A,磁场频率3 Hz,线圈匝数800匝,焊枪高度10 mm。经三线激光条纹预处理后(见图9),焊后效果如图10所示。
3.2试验结果分析
在窄间隙试验研究过程中,管道焊缝在电弧传感器和激光传感器的指引下,在侧壁上融合良好,并且前端与后端的衔接处窄坡口有折弯,前后端熔宽不一致,但焊缝贴合侧壁焊接,这是焊接系统的轨迹预测保证了焊接质量,在熔宽变化处焊接焊缝的转折也较好,说明磁控窄间隙的信息融合效果较好,视觉信号与电弧信号能够良好地融合。
试验表明,磁控窄间隙电弧视觉传感器的焊缝跟踪响应迅速,焊接质量较好,基本满足窄间隙的焊缝预测要求。对于不同宽度的窄间隙坡口,焊枪能进行稳定的焊接,同时对窄坡口间隙宽度的变化能够迅速地调整焊枪实现对中。
结论 |
(1)基于磁控电弧传感器设计了一种磁控电弧-激光相结合的传感器,并应用在焊缝跟踪系统中。两种焊缝偏差信息采用双传感器数据自适应加权融合方法进行融合处理后输入到控制系统中,然后调整焊枪位置,实现焊枪的对中。
(2)提出了一种关于窄间隙焊接的预测焊缝轨迹方法。通过前置的激光视觉传感器采集焊道信息,采用形态提取算法和基于高斯KCF 相关滤波器得到焊缝特征点的坐标,通过拉格朗日插值法拟合出焊缝轨迹的近似曲线,为双传感器信息融合的方法提供了必要条件。
(3)窄间隙焊缝跟踪试验结果表明,该传感器结构简单,工作可靠,焊缝跟踪响应迅速,焊接质量较好,为窄间隙的跟踪提供了新的技术方案。
参考文献
[1]张凯琳,苏淑靖,刘利生,等. 基于FPGA 的DDS 多路信号源设计[J]. 电测与仪表,2011,48(3):63-65.
[2]J F Henriques,R Caseiro,P Martins,et al. High-speed trackingwith kernelized correlation filters[M].IEEE Trans.,Pattern Anal. Mach. Intell.,2015,37(3):583-596.
[3]X Gao,D You,S Katayama. Seam tracking monitoring based on adaptive kalman filter embedded elman neural network during high-power fiber laser welding[J]. IEEE Trans. Ind. Electron.,2012,59(11):4315-4325.
[4]M D Graaf,R Aarts,B Jonker,et al. Real-time seam tracking for robotic laser welding using trajectory-based control[J]. Control Eng. Pract.,2010,18(8):944-953.
微信:hanlinyuanApp 传真:(021)882899521 邮箱:hanlinyuanapp#qq.com
2017-2020版权所有 不得转载 黑ICP备2023002448号