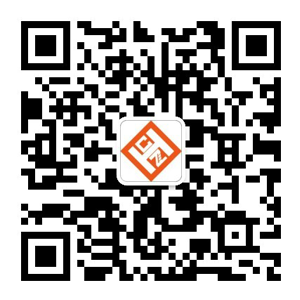
关健词:厚壁管线 焊接工艺 坡口加工
【摘要】2011年储气库注采试验地面工程是储气库总体规划建设前期试验站点,主要作用是获取XX气田南区储气库水平井注采能力、流量变化规律以及压缩机、节流阀、高压球阀、流量计等关键设备、关键技术、关键工艺的试验数据,为储气库整体建设做好前期评价工作。在整个施工过程,我们面对的主要困难为厚壁管线的焊接施工,特别是28mm和30mm厚壁管线的焊接,对于首次接触厚壁管线,从最初的坡口形式选择、组对的相关参数等方面都需要我们进行试验和探讨。
2011年,我单位施工的XX储气库注采试验地面工程为XX油田首个储气库前期试验站点,在本次施工中主要施工难点就是厚壁管线的焊接,特别是28mm和30mm厚壁管线的焊接,因此,我单位技术人员配合公司技术科及焊考办在2010年底就开始对管线的焊接工艺进行试验。经过试验确定了厚壁管线的焊接工艺。
1.1、焊接方法
1、焊接工艺
因管线壁厚较大,我们一方面要提高质量,一方面要提高工作效率,因此,我们再前期准备采用手工上向焊、半自动焊以及下向焊等方法。在整个焊接工艺的试验过程中,通过几次试验,同时考虑本次工程厚壁管线焊接工作量较少,我们采用了手工氩电联焊的方法。
1.2、焊材选用
焊材选用遵循匹配原则,本次厚壁管线材质为16Mn化肥用无缝钢管,因此焊条采用H08Mn2SiA,焊条采用E5015焊条。
1.3、试件坡口形式
施工现场我们采用单V坡口,如下图所示:
1.4、焊前清理及预热
焊前清理坡口周围≥20mm范围内的铁锈、油污以及氧化物等杂物。为改善焊缝应力,焊前对焊口进行预热处理,预热温度为100-150℃,现场采用火焰加热。预热范围以焊缝为基准中心,两侧各不小于3倍壁厚,预热因均匀防止局部过热。采用红外线测温仪对焊缝进行测量,以确保达到要求预热温度。
1.5、焊材的使用
焊条在使用前进行350℃,1.5小时的烘干,并存放在焊条保温桶中,随用随取。当天未用完的焊条应回收,重新烘干后使用,重新烘干次数不应超过两次。焊丝表面的油污等杂质应清理干净。
1.6、焊接工艺参数
焊接采用氩弧焊打底,手工上向焊焊接,每层焊道焊完后用砂轮机和钢丝刷清理焊渣后,方可进行下一层焊道焊接,每层焊道间隔不超过10分钟。具体参数见表1。
1.7、焊后保温
焊缝焊接完成后,清除焊渣,用保温被保温缓冷。
焊接工艺参数
2、现场施工实践
2.1 现场焊接人员安排
施工现场根据焊接工艺要求氩弧焊打底1道,手工电弧焊填充7道,盖面1道,打底焊1人完成,填充盖面由2名焊工同时焊接,耗时4个多小时,单个焊口需消耗焊条100根左右,打底焊材采用H08Mn2SiA焊丝,填充和盖面采用E5015焊条。
2.2 施工步骤
本次站外厚壁管线施工步骤如图所示:
施工步骤
2.3 运、布管
由于管线距离较短,全线就近设1个临时集中堆管点,用推土机平整,并堆出四条堆管带,上部放置草袋一层。现场布管时采用吊车和炮车配合进行,布管时采用尼龙吊带进行绑扎固定,将管子沿施工作业方呈锯齿形摆开,每根管子在中间处由高0.5m的草袋装细土堆撑起,首尾衔接,朝向一致,相邻管口错开1-1.5倍管径,均匀分布在施工作业带内。
2.4 管线的组焊作业
管线组焊过程严格按照焊接工艺规定进行,具体工序如下图所示:
焊接及检验工艺流程图
由于到货管材坡口角度与焊接工艺评定要求的坡口角度不符合,我们重新对坡口进行现场加工,我们采用CG2-11型磁力管道切割机,在现场对管线的坡口进行加工试验,通过试验,该型号切割机使用比较简便,且坡口成型好,速度快,因此,我们再后续的连头口的坡口加工中一直使用。(CG2-11型磁力管道切割机参数为:型号:CG2-11;机身尺寸:350×310×180mm ;输入电压:AC220V/50Hz ;切割无缝钢管直径:>108mm ;切割无缝钢管厚度:6-50mm ;切割钢板速度:50-750mm/min ;磁性吸附力:>50kg ;机器总重量:20kg。)
现场坡口加工
组对前应清理管内杂物,不得有石块、沙土等,用电动钢丝刷、锉刀等将管端20mm范围清理干净,使其露出金属光泽,但不得损伤坡口。管口组对坡口尺寸严格按照焊接工艺评定进行。
对口时,采用外对口器对口。点焊后火焰加热焊缝升温至120℃(用红外线测温仪检测),方可进行焊接作业,在组焊过程中,我们优化机组配置,打底1人,填充时2人从两边同时施焊,盖面1人,使得整道焊口的焊接时间缩短了半小时,极大的提高了工作效率。焊接完成后用保温带覆盖,待其自然冷却至室外温度时,方可拆除保温带。
焊缝填充过程
焊后保温
3、重点控制工序
3.1 坡口角度
在现场施工中,我们严格执行焊接工艺进行,首先对焊缝进行检查,因厂家到货坡口角度过大,直接焊接的话熔敷的金属截面积偏大,对于焊缝的质量有一定的影响,因此,我们再施工前对到货管材的坡口重新进行加工,以确保焊缝质量。
3.2 焊缝组对及焊前预热
焊缝组对时采用外对口器进行组对,对每道焊缝的组对间隙进行测量,以确保间隙在工艺规定范围内。点焊完成后,对焊缝进行预热,由于刚开始焊接时,我们采用一套火焰加热工具进行预热,使得整圈焊缝的预热不均匀,随后立即增加设备,从两面同时进行预热,在预热过程中,我们再达到规定温度的最高值后,进行短时间的保温,使得焊缝两侧温度达到均匀一致,更好的改善焊缝应力。
3.3 组焊过程控制
由于管线壁厚较厚,填充层数多,因此,为提高效率,必须保证焊缝的一次合格率。为此,我们在组焊过程中对每个焊工进行交底,填充的2名焊工,每层焊道焊接完成,用角向砂轮机和钢丝刷清理完焊渣后,方可进行下层焊道的焊接。同时,两名焊工同时施焊时,起弧位置应相互避开,而且下层焊道与上层焊道的起弧位置也应错开。在盖面时,由1名焊工独立完成,确保焊缝外观质量,整个焊接完成,清理表皮焊渣。
焊缝外观
3.4 焊后保温
整条焊缝焊接完成后,用保温被对焊缝进行保温,使其自然降温。通过我们再现场对以上重点工序的控制,使得厚壁管线的焊接质量得到很大提高,整条注采管线以及井场内的厚壁管线共计50道焊口,一次合格率达到98%,得到了业主及各方的肯定。
3.5 焊缝缺陷及分析
在本次施工中,注采管线全线就发生一道返修,为6点钟位置,缺陷融合,出现问题后,我们立即组织焊工对焊口进行打磨,并和检测人员在现场确定缺陷位置,最后找出未融合部位为氩弧焊打底与第一道填充金属间未融合。
因此道焊口为管线穿越处死口,在找出位置后,我们同施焊人员以及检测人员一起分析原因,主要是因为焊接电流过小,同时由于在仰焊位置,焊工焊接速度过快造成。同时,操作空间过小也对此次缺陷有影响。
4、结束语
通过焊培中心以及兄弟单位的努力,我们对厚壁管线的焊接工艺进行多次试验,并且取得了成功。同时,通过我们再现场的实践和应用,更进一步证实了焊接工艺的准确性和实用性,为整个工程的施工提供了依据,为整个工程质量的提高奠定了基础。
微信:hanlinyuanApp 传真:(021)882899521 邮箱:hanlinyuanapp#qq.com
2017-2020版权所有 不得转载 黑ICP备2023002448号